Research Projects
Development Contract
Aerodynamic component for a German vehicle manufacturer
Assignment:
The aim of the project was to develop and design a concept for the production of a one-piece sandwich component with materials made from natural and recycled fibers for the RTM process. The target was to replace the previous two-shell design with a one-piece, high-integrity concept and to investigate the influence of the top layer and core materials on Class A paintability.
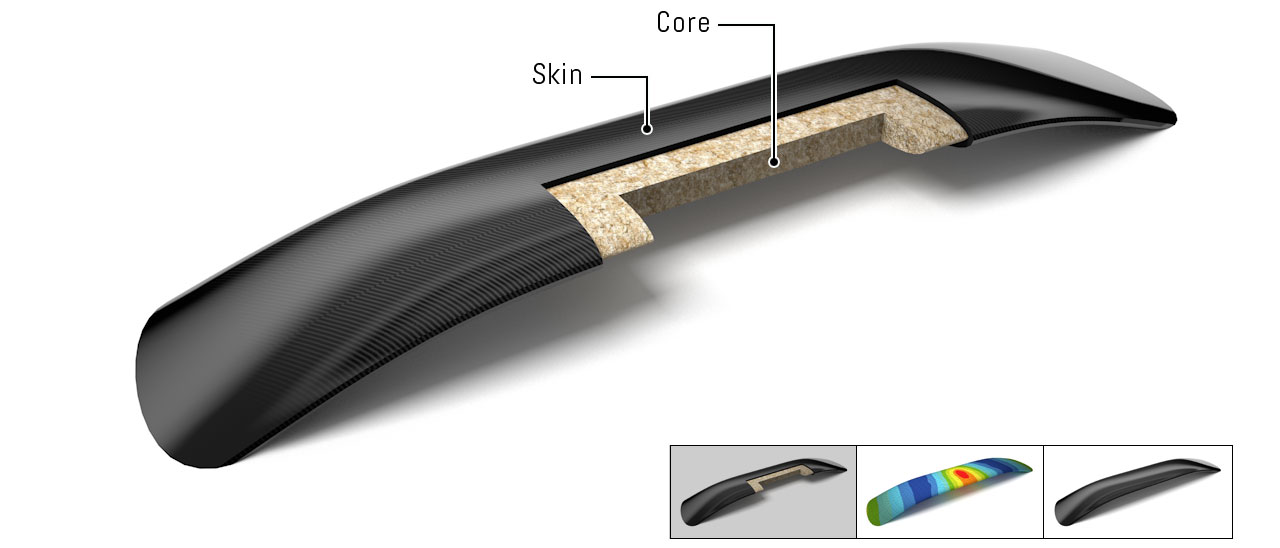

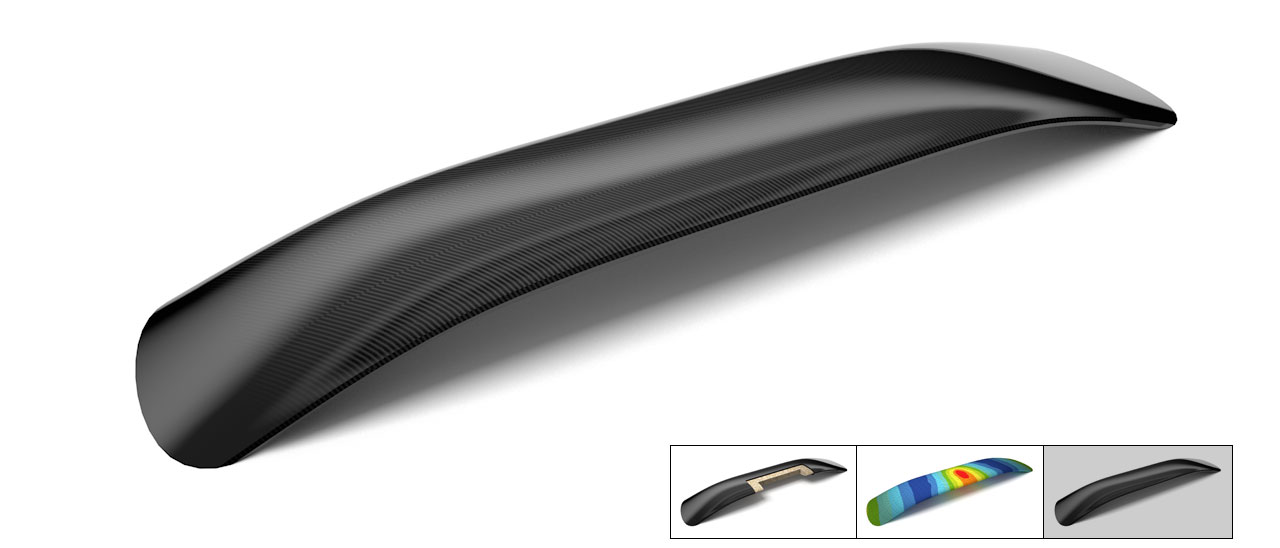
Development work:
- Investigation of various r-CF and natural fiber materials as well as different core materials in comparison with standard carbon fiber and glass fiber materials
- Design of the component for various load cases, in particular aero loads and natural frequency behavior
- Evaluation of component costs compared to conventional double-shell construction methods
Publicly Funded Projects
FST-Foampreg (2022 – 2025)
Assignment:
Development of a one-shot manufacturing process for sandwich components made with epoxy prepregs with epoxy foam cores.
Manufacturing process:
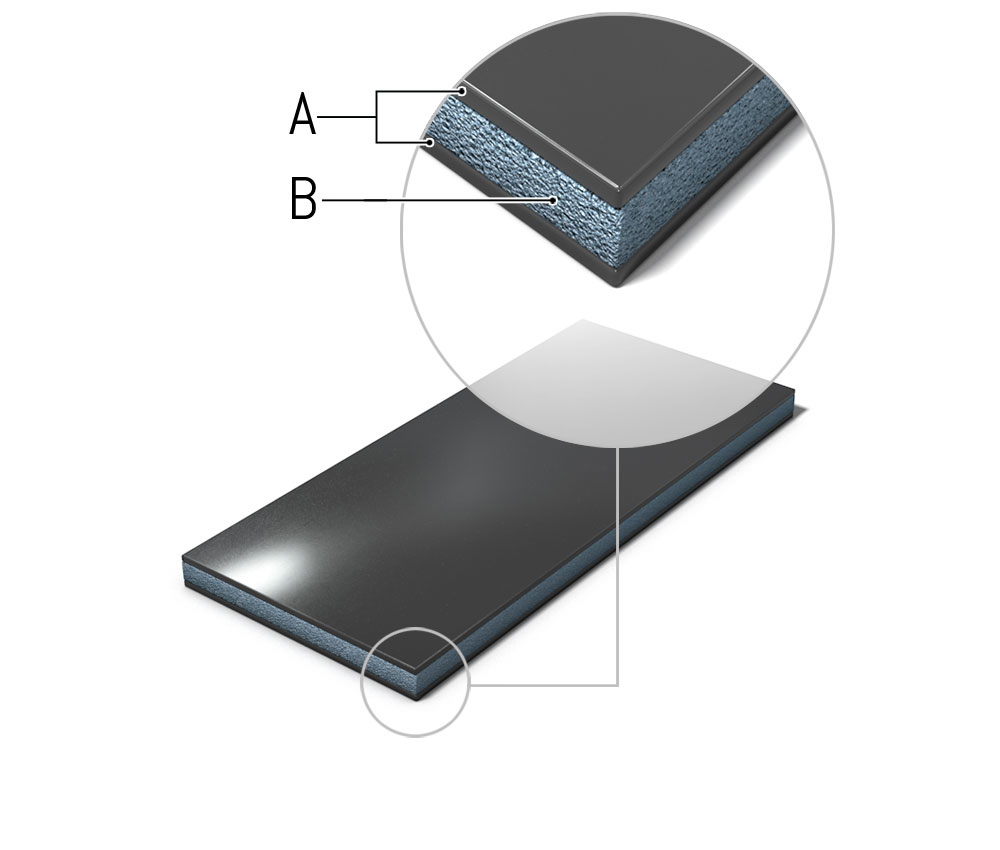
A:
Thermally latent
semi-finished
components
B:
FST-epoxy foam
incl. propellant
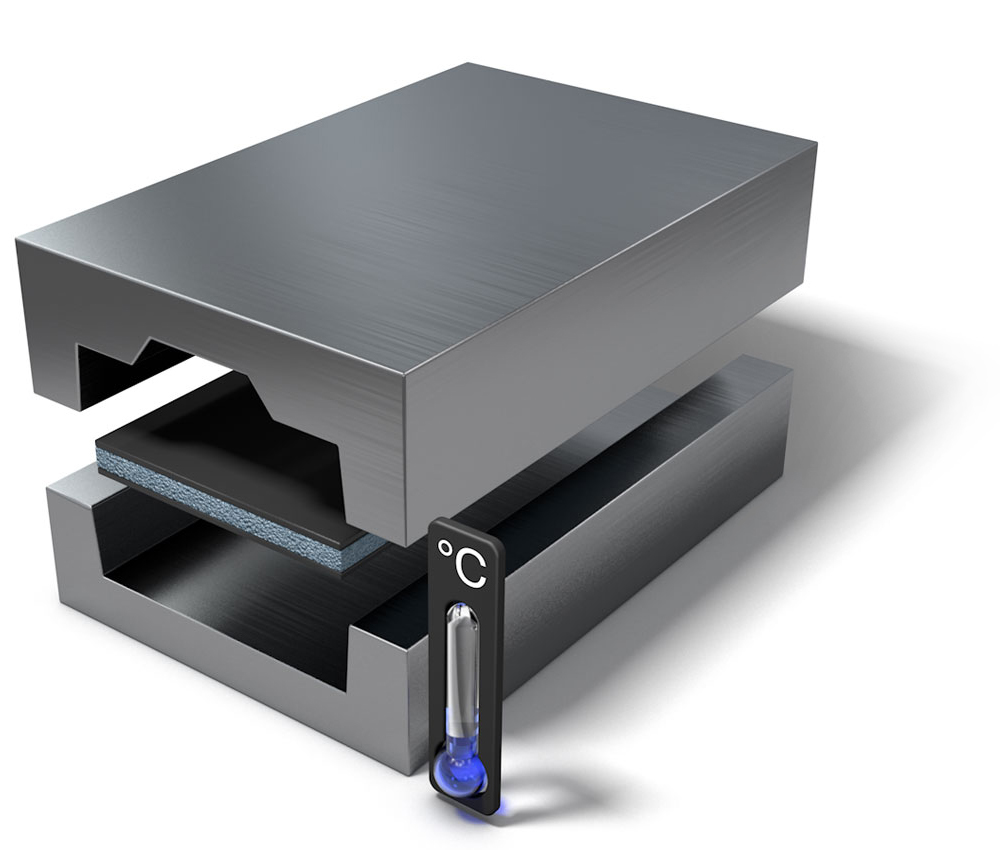
Placing of the
component in
the tool
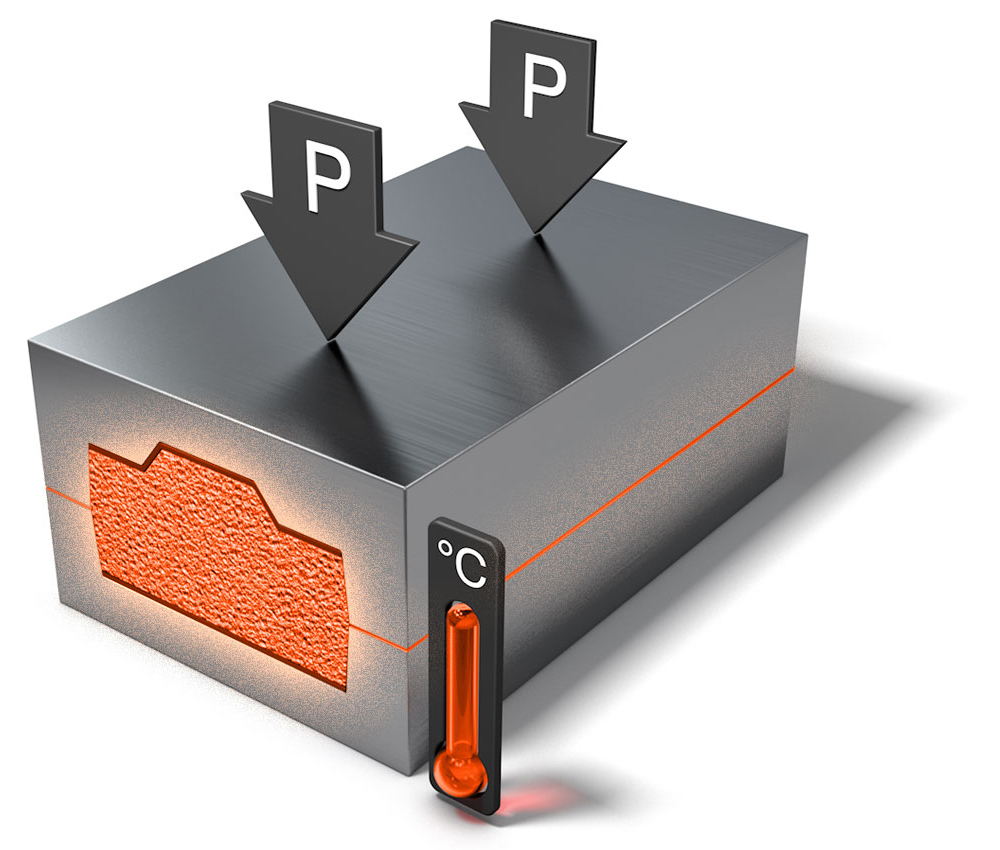
Process
activation
via pressure
and temperature
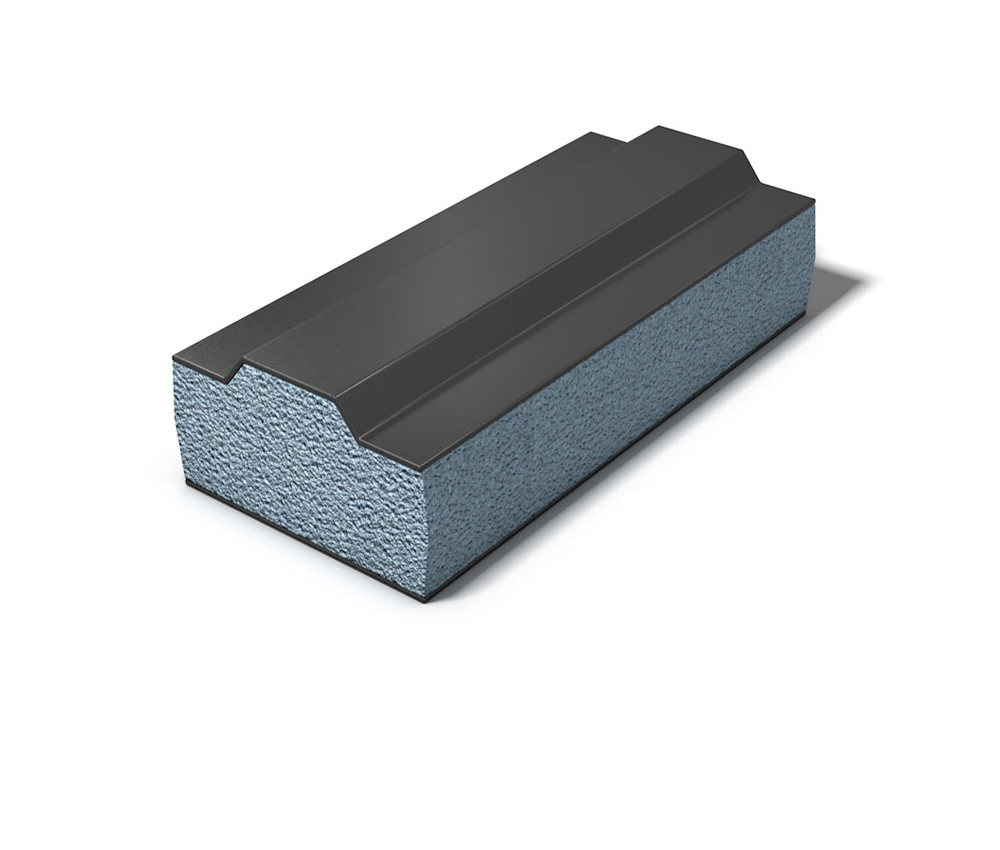
Finished
sandwich
component
Development work:
- Development of thermally latent and FST conforming prepregs and foam masses or semi-finished components
- Development of a one- or two-shot manufacturing process for autmotive, train and aviation components
- Development of a life cycle analysis and comparison of the potential environmental impact and energy balance with conventionally produced honeycomb and rigid foam structures
Gefördert durch:
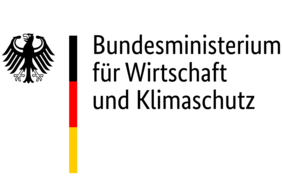
by resolution of the German Bundestag
TUCANA (2018 – 2021)
Initial situation:
Jaguar Land Rover (JLR), together with a consortium of university and industry partners, developed a lightweight chassis for electric vehicle models. The Tucana-Consortium included the Warwick Manufacturing Group (WMG), Expert Tooling & Automation, Broetje-Automation UK, Toray International UK, CCP Gransden und The Centre for Modelling & Simulation (CFMS).
Assignment:
Use of composite materials to increase vehicle rigidity, reduce weight and improve crash safety.
Influence of local reinforcement on the geometry of the chassis
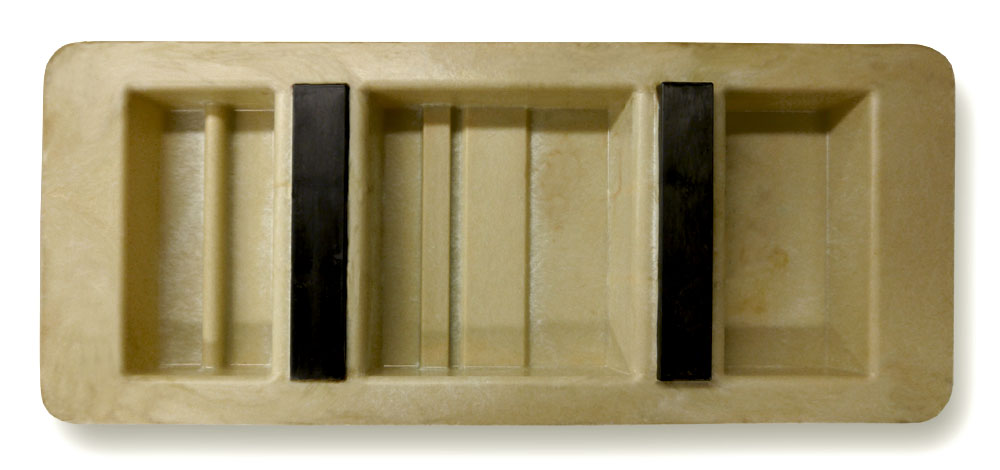
SMC-component reinforced using uni-directional carbon fiber (front)

The SMC-process makes thin and high ribs possible (rear)
Realization & result:
The aim of “Project Tucana” was to minimize vehicle weight and thus improve range and driving dynamics. For the new body, aluminum and steel were partially replaced by composite materials. This reduced the weight of the electric car by 35 kilos. At the same time, the torsional rigidity of the body increased by 30 percent thanks to the carbon fiber.
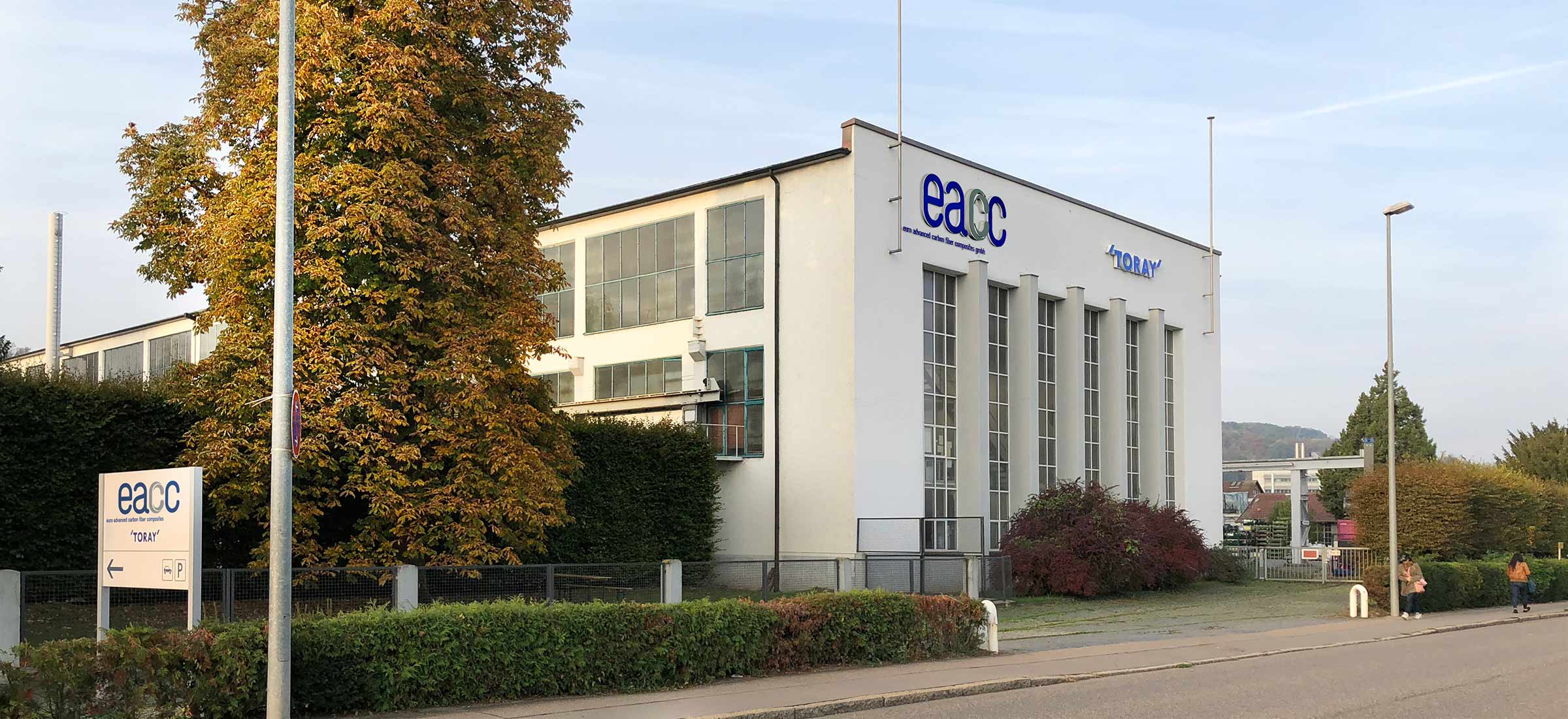